Ochrona PCB z użyciem soldermasek – część 1
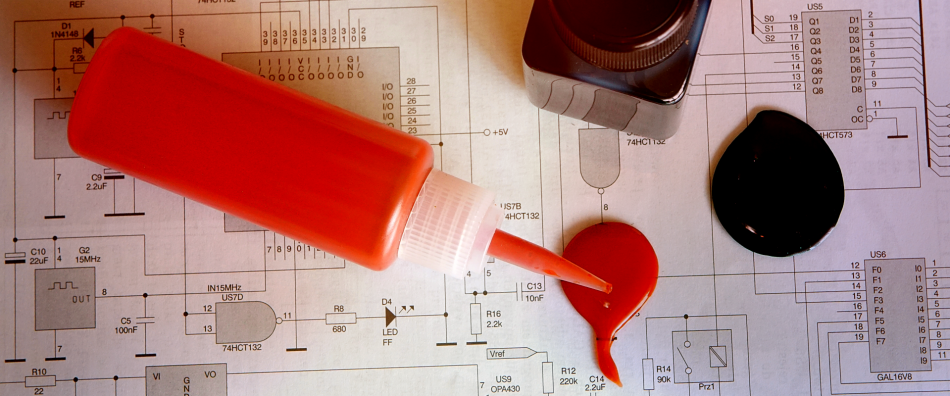
Gdy płytka drukowana będzie pracować przy niskich napięciach - rzędu kilkunastu woltów, ochrona w formie warstwy cyny lub w ostateczności roztworu kalafonii, bez lakieru zabezpieczającego może okazać się wystarczająca. Jednak w sytuacjach, gdy układ taki przewidziany jest do pracy przy wyższym napięciu, płytka drukowana powinna być wyposażona w dodatkową ochronę - tak zwaną soldermaskę. Soldermaska jest powłoką, której obecność ma bardzo dobry wpływ na wiele parametrów obwodu drukowanego, i nie jest to jedynie ograniczanie rozpływu spoiwa wyłącznie do punktów lutowniczych, czy walory estetyczne.
Gdy weźmiemy do ręki "fabryczną" płytkę drukowaną, to pierwsze co nam się rzuci w oczy to połyskująca w świetle szklista powłoka, występująca bardzo często w zielonym kolorze. To jest własnie tytułowa soldermaska.
Nie licząc oczywistych walorów estetycznych, to dzięki niej płytka drukowana zyskuje wysoką odporność na ścieranie, uszkodzenia mechaniczne, zarysowania czy stres temeraturowy. W miejsacach w których została nałożona laminat zyska bardzo skuteczną ochronę przed wilgocią, utlenianiem oraz agresywnymi związakami chemicznymi bedącymi źródłem korozji (więcej na ten temat przeczytasz w tym artykule).
Kluczowymi powodami, dla których maska lutownicza jest stosowana, to znacząca poprawa własności izolacyjnych i mechanicznych (rezystancja izolacji, odporność na przbicie), co daje projektantom możliwość zmniejszenia odległości pomiędzy ścieżkami i uzyskanie bardziej kompaktowego rozwiązania. Wytyczne w tym zakresie precyzuje norma IPC-2221, podając minimalne odległości pomiędzy ścieżkami oraz punktami montażowymi w określonych warunkach środowiskowych. Wspomniane w normie warunki środowiskowe nie są określone przez temeraturę, ciśnienie czy wilgotność powietrza, lecz powiązano je z wysokością nad poziomem morza - co w większości przypadków pozwala na szacunkowe opisanie właściwości izolacyjnych powietrza. Szacunki w stosunku do płytek drukowanych bez powłoki stanowią pewien kompromis mający na względzie fakt, że wraz ze wzrostem wilgotności powietrza rośnie "upływność" pomiędzy ścieżkami, natomiast gdy wilgotność powietrza maleje automatycznie rośnie ryzyko przeskoku elektrostatycznego.
By nie odbiegać zbytnio od tematu i nie bazować wyłącznie na abstrakcie, wyobraźmy sobie płytkę drukowaną prostego regulatora fazowego, pracującego przy napięciu sieciowym 230V. Bez żadnej powłoki ochronnej na terenie zlokalizowanym do 3000 m.n.p.m. będzie ona wymagała odległości między scieżkami w wymiarze minimum 1,25 milimetra. Ta sama płytka pokryta maską lutowniczą, bedzie wymagała już tylko 0,4 milimetra. Jeśli układ nie zakłada zbyt dużych obciążeń, a tym samym dużych szerokości ścieżek, to nie powinno być problemu z zachowaniem bezpiecznej odległości pomiędzy nimi w drodze do zacisków montażowych (np: złącza ARK o rastrze 200mils = 5,08mm). Jeśli jednak obciążenie ma być większe, powiedzmy 10A (co dla regulatora fazowego nie jest niczym nadzwyczajnym), bez maski lutowniczej możemy mieć problem z uzyskaniem kompromisu pomiędzy wymaganą szerokością obciążanych ścieżek a odległością między nimi.
A co w sytuacji gdy podany w przykładzie układ pracuje w środowisku o bardzo małej wilgotności, tym samym podatność szczeliny powietrznej na przebicie jest zdecydowanie większa? - Dla płytki pokrytej soldermaską nic się nie zmieni natomiast dla płytki bez tej powłoki pojawi się wymóg stosowania odstępów w wymiarze 12,5 milimetra, co sprawi, że nie będzie możliwe zaprojektowanie zwartej konstrukcji.
Przebiegły elektronik pomyśli "mój układ będzie pracował w domu a nie na Saharze, zgodnie z normą uwzględnie więc przerwę 1,25 milimetra" - przy takim założeniu teoretycznie nic się nie powinno dziać. Ale tylko teoretycznie, bo z czasem płytka pokryje się warstewką kurzu, która w połączeniu z wilgocią i innymi zanieczyszczeniami z powietrza będzie mieć coraz lepsze warunki do tak zwanej elektrokorozji, elektromigracji a nawet zgubnych zwarć lub przebić.
W pierwszej części tego artykułu poruszę zagadnienie metod bazujących na materiałach potocznie stosowanych do malowania szkła i ceramiki
... Zapraszam do lektury.
Farby do szkła wypalane w piecu
W metodzie tej za pomocą pędzelka (najlepiej nylonowego) nanosimy możliwie cienką warstwę gęstej farby do szkła lub ceramiki, suszymy przez kilka godzin a następnie wypalamy w temperaturze 140-150OC. Po wypalaniu na całej powierzchni płytki otrzymujemy twardą i niezbyt równą szklistą powłokę. Dalej czeka nas "już tylko" czasochłonne zdrapywanie farby z punktów lutowniczych z użyciem ostrego narzędzia.
Jeśli chodzi o wykonanie to jest to wszystko co trzeba wykonać. Sama powłoka pozostawia jednak wiele do życzenia. Dlaczego? Farba do szkła została stworzona do zgoła innych celów i trudno mówić o jej odporności na przebicie czy na temeratury rzędu 260OC, jakie występują podczas lutowania. Zazwyczaj farby do szkła i ceramiki po wypaleniu są nie tylko twarde ale i kruche, co podczas zmian temperatury powoduje jej pękanie i odpryski. Im grubsza wartwa tym bardziej podatna jest na odpryski, nawet podczas usuwania niechcianej farby z padów. Niejednokrotnie spękania są obecne już po wypalaniu utwardzającym. Walory estetyczne takiej powłoki są raczej wątpliwe, poodobnie jak i właściwości ochronne. Koszty takiego rozwiązania (15-20PLN za 50 mililitrową buteleczkę) również nie są zachęcające, tym bardziej, że wydajność farby jest niewielka (1-2 płytki dwustronne formatu A4 z 50ml specyfiku) a w niższej cenie (w przeliczeniu na jednostkę objętości) można zakupić profesjonalne preparaty.
- łatwo dostępne materiały do nanoszenia
- wysokie ceny farb do szkła przeznaczonych do wypalania
- mała wydajność farby
- proces jest czasochłonny i kłopotliwy (metoda wymaga drapania padów które mają być odsłonięte)
- gdy farba się zeszkli po wypalaniu jest twarda lecz krucha i tym samym podatna na odpryski
- powłokę należy traktować raczej jako imitacja soldermaski, powłoka pod względem elektrycznym i mechanicznym nie spełnia żadnych norm
- łatwo ulega uszkodzeniu podczas lutowania
- ze względu na pozostałości farby na padach, lutowanie jest utrudnione
Lakier En-solder - mechaniczne usuwanie nadmiaru maski
Bez zbędnego rozpisywania się, proces nanoszenia przebiega dokładnie tak samo jak w przypadku farb do szkła (sam En-solder z wysokim prawdopodobieństwem jest farbą do szkła). Jedyną różnicą jest zastosowanie do tego celu lakieru En-Solder. Lakier ten, według informacji udzielanych przez dystrybutora, to preparat na bazie polimerowo-kauczykowej i po nałożeniu pędzlem nylonowym należy go wypalić w temeraturze 170-180OC przez 15 do 25 minut.
W porównaniu z farbami do szkła powłoka jest cieńsza i wizualnie lepsza, jednak wciąż brakuje jej wiele do ideału. Po jej nałożeniu można wszakże liczyć na dobrą ochronę przed korozją ale własności mechaniczne czy izolacyjne pozostawiaja wiele do życzenia. Podobnie jak w przypadku farb do szkła, trudno mówić o zgodności z jakimikolwiek normami. Pisząc o tym rozwiązaniu należy również wspomnieć o problemie przyklejania się spoiwa do tej "maski lutowniczej". Dystrybutor deklaruje wydajność na poziomie dwóch dwustronnych płytek formatu A4 z 20 mililitrów lakieru, wypada zatem nieco lepiej niż farba do szkła. Przechodząc do aspektów ekonomicznych to za 20 mililitrowy pojemniczek w 2010 roku trzeba było zapłacić 10 złotych. Preparat obecnie jest niedostępny w sprzedaży.
- łatwo dostępne materiały do nanoszenia
- dobra ochrona antykorozyjna
- Przy zachowaiu staranności względnie estetyczna powłoka
- w przeliczeniu na jednostkę objętości cena jest wyższa niż farb do szkła
- lakier na chwilę obecną niedostępny w sprzedaży
- mała wydajność (choć większa niż typowych farb do szkła)
- podczas lutowania spoiwo lepi się do maski
- proces jest czasochłonny i kłopotliwy (metoda wymaga drapania padów które mają być odsłonięte)
- powłokę należy traktować raczej jako imitacja soldermaski, powłoka pod względem elektrycznym i mechanicznym nie spełnia żadnych norm
- ze względu na pozostałości farby na padach, lutowanie jest utrudnione i wymaga dużej ilości topnika
Lakier En-solder - zmywanie nadmiaru maski acetonem
Metoda bazuje na wykorzystaniu lakieru En-Solder, jednak by przyśpieszyć i ułatwić usuwanie farby z padów, autor metody zaproponował takie oto rozwiązanie. W pierwszej kolejności zabezpieczamy pady tonerem nakładanym metodą termotransferu, po czym delikatnie malujemy płytkę pędzlem nylonowym, w kolejnym kroku podsuszamy powłokę w temeraturze 160-170OC przez 10 minut, by po ostygnięciu potraktować ją acetonem. Przy odrobinie szczęścia farba z padów zejdzie wraz z tonerem prędzej niż z reszty płytki. Gdy ten manewr się uda, należy ją całkowicie wysuszyć w piecu.
Co dzięki takiemu zabiegowi zyskujemy? Teoretycznie szybszy proces wykonania płytki, a jeśli mamy mniej szczęścia musimy zmyć całość i próbowac jeszcze raz. Mi osobiście, nigdy nie udało się uzyskać zadowalających efektów tą metodą, bo jak w przypadku mechanicznego usuwania padów powłoka była względnie ładna gładka i czysta, tak tutaj pozostaje jedynie kolor, a sama powłoka jest matowa, chropowata i zabrudzona resztkami tonera. Własności mechaniczne i elektryczne pozostają na tym samym, kiepskim poziomie. W porównaniu z mechaniczną metodą usuwania lakieru z padów, w tym rozwiązaniu spora część lakieru staje się odpadem a jego wydajność realnie spada.- łatwo dostępne materiały do nanoszenia
- dobra ochrona antykorozyjna
- "brudny" proces usuwania nadmiaru maski z padów, pozostawiający sporo zanieczyszczeń we właściwej powłoce
- gotowa powłoka jest matowa i chropowata, nie zachowując ostrych krawędzi odcięcia.
- podczas zmywania maski z padów istnieje bardzo duże prawdopobieństwo zmycia farby z obszarów które powinny być pokryte, i tym samym wymusza konieczność powtórzenia procesu
- w przeliczeniu na jednostkę objętości cena jest wyższa niż farb do szkła
- lakier na chwilę obecną niedostępny w sprzedaży
- mała wydajność farby
- podczas lutowania spoiwo lepi się do maski
- proces jest czasochłonny i kłopotliwy (metoda wymaga drapania padów które mają być odsłonięte)
- powłokę należy traktować raczej jako imitacja soldermaski, powłoka pod względem elektrycznym i mechanicznym nie spełnia żadnych norm
- ze względu na pozostałości farby na padach, lutowanie jest utrudnione i wymaga dużej ilości topnika
Artykuły z tej serii
Jeśli jesteś zainteresowany innymi metodami zapraszam do kolejnych artykułów.
- CZĘŚĆ 1 - Cel stosowania soldermasek, Soldermaski wykonywane farbami do szkła
- CZĘŚĆ 2 - Soldermaski w formie folii
- CZĘŚĆ 3 - Soldermaski UV
- CZĘŚĆ 4 - Soldermaski fotobrazowe
- CZĘŚĆ 5 - Podsumowanie wszystkich metod nakładania soldermasek