Ochrona antykorozyjna PCB przez cynowanie
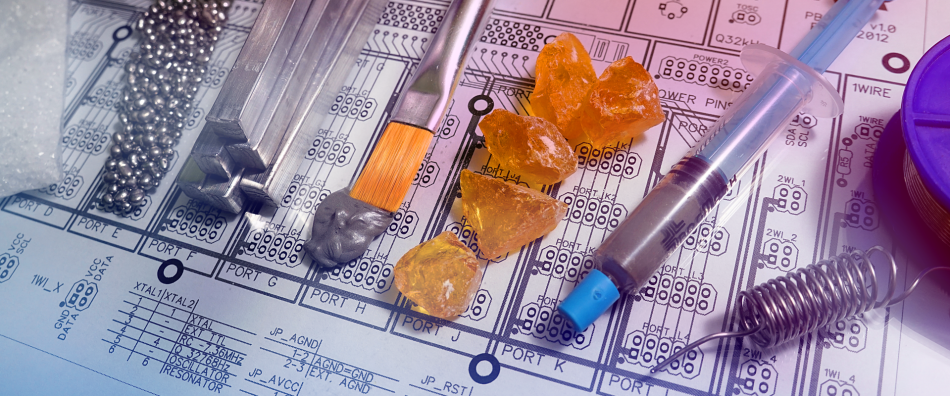
W poprzednim artykule wyjaśniłem mechanizmy korozji z jakimi zmagać się musi odsłonięta powłoka miedzi, oraz konieczności jej ochrony przed czynnikami zewnętrznymi. Przemysłowa produkcja płytek drukowanych opiera się na sprawdzonych rozwiązaniach bazujących na wytrzymałych soldermaskach, powlekaniu srebrem i złotem oraz cynowaniu zanurzeniowym metodą HAL. Co jednak zrobić, gdy układy wykonujemy amatorsko, lub gdy zależy nam na wykonaniu krótkiej serii czy nawet pojedynczych sztuk?
Oczywiście po wykonaniu płytki, możemy ją doraźnie zabezpieczyć za pomocą roztworu kalafonii i alkoholu. Taką metodę stosuje wielu hobbystów, jednak muszą oni brać pod uwagę długi czas jej schnięcia, oraz to, że w zależności od warunków zewnętrznych powłoka jest albo krucha albo lepka. Na domiar złego, kalafonia jest topnikiem pełniącym w elektronice inne zadanie, i pozostawiona na powierzchni płytki drukowanej w perspektywie czasu może sama stać się ogniskiem korozji, wszystko za sprawą Kwasu Abietynowego - C20H30O2, który w kalafonii stanowi czynnik aktywny.
Inne źródła sugerują stosowanie dedykowanych do tego celu lakierów ochronnych (np: Plastik 70, Urethan 71), jednak po ich zastosowaniu modyfikacje płytek lub wymiana uszkodzonych elementów, jest kłopotliwa.
Jeśli nie jesteśmy zainteresowani stosowaniem soldermasek (o których napisze przy okazji kolejnych artykułów), pozostają nam do wyboru metody bazujące na stopach i pastach lutowniczych - ich zestawienie przedstawiam poniżej :
Cynowanie płytki typowym stopem lutowniczym za pomocą lutownicy
Jedyne co jest potrzebne w tej metodzie to zwykła cyna oraz topnik (na przykład kalafonia, pasta lutownicza lub RF800). Samo nanoszenie cyny na powierzchnię nie jest skomplikowane, ale przy większych płytkach może okazać się czasochłonne. Co więcej gdy dysponujemy jedynie lutownicą transfomroatorową i nie zastosujemy zalecanych przez jej producenta przerw w pracy, możemy ja nadzwyczajniej spalić. Proces można sobie ułatwić przez użycie szerokiej plecionki, która powiększy cynowany w danej chwili obszar. Plecionka pełni również funkcje magazynu niewielkiej ilości cyny oraz topnika. Przegladając internet można się również natknąć na modyfikacje lutownic kolbowych, w których zwykły punktowy grot zastąpiony jest miedzianą "płetwą". Stosując jednak takie rozwiązania trudno mówić o kontroli temperatury, a gdy ta jest zbyt wysoka o uszkodzenie płytki jest bardzo łatwo.
- metoda nie wymaga żadnych dodatkowych, narzędzi poza tymi które już się posiada
- stosowany jest standardowy i niedrogi stop LC60 (w cenie 35pln za 250gram)
- powstaje powłoka metaliczna o bardzo dobrej lutowalności również po dłuższym czasie
- czasochłonny proces nanoszenia
- konieczność stosowania dużych ilości topników, które następnie należy usuwać
- podczas pracy wydziela się dużo szkodliwych oparów topnika
- istnieje ryzyko przegrzania cienkich ścieżek a w efekcie ich zerwanie lub odklejenie od laminatu
Cynowanie w tyglach
Cynowanie z użyciem wanien, rynien czy tygli nie jest nowością w przemyśle elektronicznym. Wszędzie tam gdzie odbywają się procesy cynowania HAL (Hot Air Levelling) czy lutowanie na fali mamy do czynienia z takim rozwiązaniem. W warunkach domowych takie rozwiązania, oczywiście na niewielką skalę, również są możliwe. Trzeba mieć jednak na uwadze, że nawet niewielkie tygielki umożliwiajace pocynowanie niedużych płytek do najtańszych nie należą (ceny tygli o wymiarach wanny 9x13cm zaczynają się od 1000PLN) i wymagają wsadu o wadze nie mniejszej niż 2-3 kilogramy. Mniejsze tygle z racji cylindrycznego kształtu wanny nie są użyteczne podczas cynowania płytek, a ich eksploatacja ogranicza się zazwyczaj do pobielania końcówek przewodów.
- bardzo skuteczne i szybkie
- powstaje powłoka metaliczna o bardzo dobrej lutowalności również po dłuższym czasie
- wymaga kosztownego osprzętu
- wymaga dużej ilości stopu lutowniczego, który z czasem może uledz zanieczyszczeniu
- z racji gabarytów i cen tygli metoda stosowana zazwyczaj do pobielania przewodów, sporadycznie do cynowania niewielkich płytek
Cynowanie z użyciem pasty lutowniczej do lutowania SMD
Asortyment past do lutowania SMD na rynku jest bardzo szeroki. Dostępne są takie na bazie spoiw ołowiowych jak i bezołowiowych, wiele z nich nie zawiera topników na bazie chlorków a więc nie wymagają czyszczenia płytki po procesie. Samo użycie ogranicza się do aplikacji pasty za pomocą strzykawki i podgrzaniu płytki za pomocą stacji na gorące powietrze (ang: HotAir), lub w Piecu do lutowania rozpływowego (ang: Reflow Oven) lub domowych adaptacji piekarników kuchennych z elektronicznym regulatorem. Przed szerszym stosowaniem tej metody skutecznie powstrzymują dość wysokie ceny, rozpoczynające się zazwyczaj od 10PLN za kilkunasto gramową strzykawkę z pastą.
- powłoka metaliczna o bardzo dobrej lutowalności również po upływie dłuższego czasu
- Możliwość zestalania powłoki w piekarnikach lub z użyciem stacji hotair
- łatwe ale czasochłonne nanoszenie za pomocą strzykawki
- bardzo wysokie ceny past do lutowania rozpływowego
Cynowanie pastami Sn97Cu3 do lutowania rur C.O.
Chwilę temu wspomniałem, że pasty do lutowania rozpływowego SMD byłyby bardzo dobrą alternatywą do zabezpieczania płytek drukowanych przed korozją. Byłyby, gdyby nie kluczowe w tym przypadku kryterium jakim jest cena. Kryterium ceny jest również głównym powodem dla którego elektronicy amatorzy, sięgają po artykuły takie jak na przykład Amasan LF3, Bisan LB3 czy Rothenberger ROSOL3. Przy cenie od 20PLN za opakowanie 100gram, można sobie pozowlić na równomierne przesmarowanie całej płytki drukowanej i wygrzanie jej w temeraturze bliskiej 300OC, by po czyszczeniu uzyskać równomiernie pobieloną powłokę. Wszysto byłoby w porządku gdyby nie to, że produkty przeznaczone do lutowania miedzianych instalacji centralnego ogrzewania, to spoiwa bazujące na agresywnym topniku jakim jest Chlorek Cynku - ZnCl2. Stosując takie pasty wyrządzamy Swoim realizacjom więcej krzywdy niż pożytku - pisałem już o tym w artykule poświęconemu korozji miedzi. Jakby tego było mało chlorek cynku zawarty w paście w podwyższonej temeraturze niszczy powierzchnię soldermasek przeznaczonych do nakładania laminatorem (topnik powoduje matowienie i głębokie wżery na jej powierzchni). Fakt ten potwierdził się w przypadku dostępnych na polskim rynku soldermasek do laminowania, oraz przemysłowej soldemrasce DuPont (w kolorze ochry).
- duża szybkość wykonania płytki
- korzystne ceny pasty w stosunku do dedykownych past SMD (od 45pln za 250gram)
- łatwe nanoszenie za pomocą pędzelka lub szpatułki
- możliwość zestalania powłoki w piecach, z użyciem stacji HotAir lub Opalarki
- po procesie nanoszenia powłoka jest matowa a z racji jej silnego utlenienia lutowalność jest nienajlepsza i ulega pogorszeniu z upływem czasu
- agresywny i bardzo reaktywny topnik - chlorek cynku ZnCl2 - który jest katalizatorem korozji chlorkowej scieżek
- chlorek cynku ma tendencje do bardzo szybkiego rozpuszczania warstwy miedzi w temperaturach bliskich 300OC
- w przypadku grzania płytki w niższych temeraturach powłoka jest bardzo cienka
- chlorek cynku zawarty w paście niszczy powierzchnię soldermasek nakładanych laminatorem
- konieczność bardzo dokładnego płukania, najlepiej neutralizacji w roztworze sody lub mleka wapiennego
Cynowanie chemiczne bezprądowe
Reakcja jaka ma miejsce w tym procesie jest reakcją wymiany pomiędzy metaliczną miedzią a cyną zawartą w Chlorku Cyny(II) - SnCl2. Proces ten zachodzi w środowisku kwaśnym w obecności Tiomocznika - CH4N2S, który kompleksuje jony metalu, prowadząc do odwrócenia potencjałów metali biorących udział w reakcji. Na takim modelu reakcji bazują dostępne na rynku gotowe środki do cynowania chemicznego, a najpopularniejsze z nich to TANNAL ImmerTinn, SENO-3211 oraz AGT-086. Roztwór do bezprądowego cynowania można przygotować również samodzielnie korzystając z receptury:
- 1,3g - Chlorku Cyny(II) - SnCl2,
- 12,5g - Tiomocznika - CH4N2S,
- 8,8g - Kwasu Winowego - C4H6O6,
- oraz 250ml wody Destylowanej lub demineralizowanej H2O.
W początkowej fazie osadzanie się metalicznej cyny jest dość szybkie i pierwsze 1.5-2.0μm powłoki powstaje w kilka minut. Gdy powierzchnia miedzi pokryje się już szczelną warstwą cyny reakcja drastycznie zwalnia i na kolejne mikrometry powłoki trzeba czekać od kilkudziesięciu minut do kilku godzin. Stopień zużycia roztworu również wywiera wpływ na czas tworzenia się powłoki. Producenci preparatów zalecają odtłuszczenie powłoki, jednak w rzeczywistości dobre efekty uzyskuje się dopiero po dokładnym wypolerowaniu powierzchni miedzi. Gdy płytka posiada soldermaskę, krawędzie otworów mają zadziory, powierzchnia miedzi posiada wżery po trawieniu, możliwości polerowania powierzchni miedzi są ograniczone, a powłoka ochronna wytworzy się selektywnie, definiując jej złą jakość. Bez względu na to czy kąpiel cynującą przygotowujemy samodzielnie, czy rozrabiamy ją z gotowego preparatu, musimy się liczyć z jego ograniczoną żywotnością, ponieważ znajdujący się w roztworze aktywny chlorek cyny(II) SnCl2 w krótkim czasie hydrolizuje i strąca się w formie nierozpuszczalnego wodorotlenku cyny Sn(OH)2.
- powierzchnia powłoki lustrzana i bardzo estetyczna, o ile zachowa się perfekcyjną czystość, oraz dokładnie wypoleruje powierzchnię miedzi
- dobra lutowalność zaraz po wykonaniu procesu cynowania
- lutowalność powłoki w krótkim czasie znacznie się pogarsza
- roztwór cynujący zawiera toksyczny tiomocznik
- w zależności od stopnia zużycia preparatu, oraz grubości powłoki jaką chce się uzyskać proces może trwać od kilku/kilkunastu minut do kilku godzin
- wysoka cena preparatu do cynowania
- przygotowany preparat traci z czasem swoje własności
- konieczność zachowania wysokiej czystości kąpieli cynującej (niezbędne jest rozrabianie preparatu w wodzie demineralizowanej lub destylowanej)
- mała wydajność (jedna torebka wystarcza raptem na kilka niedużych płytek)
- konieczność perfekcyjnego przygotowania powierzchni miedzi z polerowaniem włącznie
- uzyskanie dobrej jakości powłoki jest utrudnione a czasem niemożliwe
Cynowanie niskotopliwym stopem Lichtenberga we wrzątku
Na sam koniec chciałbym przedstawić najmłodszy ze wszystkich sposób zabezpieczania płytek drukowanych przed korozją. Jego historia rozpoczęła się od pewnego rosyjskiego artykułu z 2009 roku, a na polskim forum branżowym, pojawiła się o niej jedynie krótka wzminaka. Metoda, mimo że zadziwiajaco prosta, na tamten czas nie przyjęła się, głównie za sprawą problemów z dostępnością wspomnianego w artykule stopu Rosego.
Nie będę ukrywał, że metoda na dobre zawitała na polskim rynku za sprawą mojej własnej aktywności w tym temacie. W efekcie wielu tygodni testów i doswiadczeń bazujących na samodzielnie przygotowywanych próbkach różnych mieszanek metali, stop z rosyjskiej publikacji został wyparty przez stop Lichtenberga. Metoda zyskała na popularnosci, gdy w ramach prowadzonej działaności gospodarczej, dopracowałem technologię wytwarzania tego stopu w wygodnej do dozowania formie i wprowadziłem go do obrotu handlowego za pośrednictwem serwisu aukcyjnego allegro, eliminując tym samym problem jego dostępności na polskim rynku.
Metoda pobielania ścieżek tym sposobem polega na rozprowadzeniu stopu po powierzchni PCB, a następnie usunięciu jego nadmiaru, w gotującej się wodzie. Nie licząc łatwego do kupienia stopu Lichtenberga, potrzebny jest jedynie kwasek cytrynowy (w roli topnika) oraz najzwyklejsza woda. Za źródło ciepła wystarczy kuchenny piec gazowy lub elektryczny, a naczyniem w którym przystąpimy do cynowania może być wysłużony garnek nierdzewny, naczynie żaroodporne a w ostateczności nawet puszka. Powłoka jaka w ten sposób powstaje, skutecznie chroni przed korozją i ma bardzo dobrą lutowalność, nawet po 3 latach od przeprowadzonego cynowania! Sam stop jest na tyle wszechstronny, że może posłużyć również do lutowania podzespołów wrażliwych na temeraturę (np. diody laserowe), a nawet posłużyć do wylytowywania układów SMD o dużej ilości wyprowadzeń, stanowiąc dużo tańszą alternatywę dla takich produktów jak np. ChipQuik. Jeśli na siłę zaczniemy szukać minusów tej metody to wykryjemy jedynie wpływ na obniżenie temperatury topnienia spoiny, który będzie miał miejsce jedynie wtedy, gdy nie usuniemy nadmiaru stopu z powierzchni powlekanej miedzi. Gdy postąpimy zgodnie z instrukcjami i zostawiamy jedynie bardzo cienką powłokę, wspomniany wpływ jest pomijalnie mały.
- bardzo dobra lutowaloność powłoki, również po upływie bardzo długiego czasu
- powłoka o jakości porównywalnej do przemysłowo stosowanej metody HAL
- połyskliwa i bardzo estetyczna powierzchnia powłoki
- brak ryzyka przegrzania płytki
- bardzo duża wydajność przy pokrywaniu stopem, wyższa niż podczas cynowania zwykłym stopem LC60
- niska cena stopu Lichtenberga (około 32PLN za 100gram)
- brak konieczności stosowania drogich odczynników (jedynie woda i kwasek cytrynowy)
- krótki czas przygotwania do cynowania, jak i sam proces (po zagotowaniu wody z kwaskiem, cynowanie trwa kilka/kilkanascie sekund)
- brak szkodliwych oparów podczas procesu
- niewielki wpływ na obniżenie temeratury topnienia spoiny
Podsumowanie
Zestawiając ze sobą wszystkie za i przeciw każdej przedstawionej metody, wybór najlepszego dla siebie rozwiązania nasuwa się sam.